Using Big Data analytics in maintenance resembles the fourth level of maturity in predictive maintenance. This fourth level is called Predictive Maintenance 4.0, or PdM 4.0.
PdM 4.0 is concerned with predicting future defects in assets and eventually prescribing the most effective preventive measures, by applying advanced analytical techniques on Big Data. Big Data is collected from numerous aspects of the assets such as technical condition, use, environment, maintenance history, comparable equipment elsewhere, and all other aspects that possibly contribute to the performance of the concerning asset.
Four levels of maturity distinguished within Predictive Maintenance:
- Level 1. Visual inspections: periodic physical inspections. During this inspection, conclusions are solely based on the expertise of the inspector.
- Level 2. Instrument inspections: periodic inspections. During these inspections, conclusions are based on the expertise of the inspector, combined with the measured value of our instruments.
- Level 3. Real-time condition monitoring: continuous real-time condition monitoring of assets, during which alerts are being send out if a predetermined critical level is reached.
- Level 4. PdM 4.0: continuous real-time monitoring of assets. Critical levels are based on predictive techniques, such as regression analysis and are most commonly based on a combination or correlation of different measurement values.
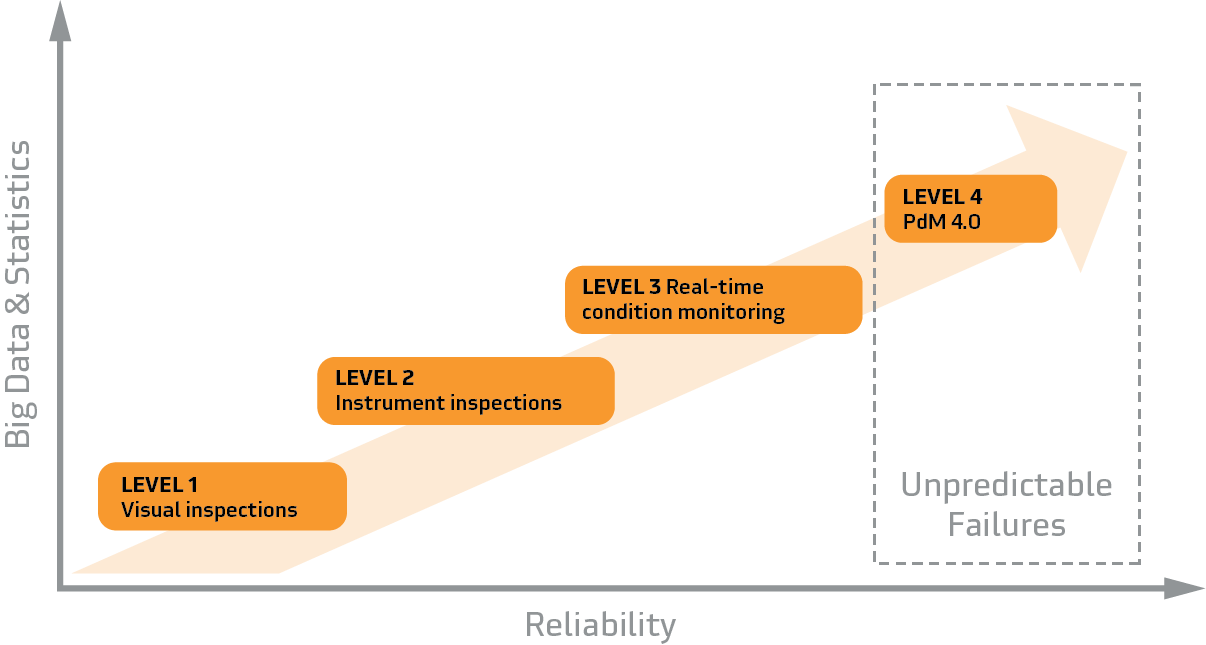
Success factors critical for the implementation of PdM 4.0:
- The most important critical success factor (CSF) is the availability of data. Technology would be the second most important.
- The availability of data is critical, because one of the biggest technological challenges still holds the collection of continuous and real-time sensor data of numerous assets.
- Multiple parts of outdated asset bases are not yet provided with the necessary sensors.
- The capacity of data networks during collection of large quantities of data, is a demanding concern. Especially for data that concerns fleet of trucks and trains, who cover large areas during their trip.
- In addition to this concern, dangerous industrial environments require an IOT-infrastructure which is specifically designed to meet certain safety demands.
A successful implementation of PdM 4.0 features the following steps:
- Asset Value Ranking & Feasibility Study. In this step, assets that are worth applying PdM 4.0 to are identified, with the purpose of enlarging the reliablity of the assets.
- Asset selection for PdM 4.0. Select assets that can be used in pilot projects, learn from its results and apply these findings when PdM 4.0 is used on other asset types.
- Reliability Modelling: Root Cause Analysis (RCA) and Failure Mode Effect Analysis (FMEA) per asset type to guide our clients in the right direction. Which data is necessary to determine the required sensor data and external datasets.
- PDM Algorithm Design. This is the true highlight of data analytics. Choosing the right algorithm is the most important factor when making predictions and thus the quality of predictions. Choosing can be relatively easy, but in some cases advice from specialists or scientists is required, when producing more complex models.
- Real Time Performance Monitoring. This is the true launch of the PdM 4.0 model. The algorithm processes data from different sources to monitor the real-time condition of an asset.
- Failure Prediciton. The algorithm is able to predict future defects. Acting upon these predicitions can require – especially in the beginning – a certain degree of faith and is therefore usually completed with own insights.
- Predictive task prescription. At the highest level of PdM 4.0, the algorithm does not only forecast when a defect will occur, but also which correcting measures should be taken. These measures are chosen from a vast array of tasks (library of tasks).
Want to improve your Maintenance & Asset Management organisation?
Contact us and let’s get started.
Social